UDMhp/ba
1 to 3 drives, 85-265Vac, up to 15/30A
EtherCAT ® Drive Module, Compact, Powerful
- EtherCAT Universal Drive Module with up to 3 built-in drives
- Two versions: Economical (ba) and High Performance (hp)
- Three built-in drives
- 85 to 265Vac, up to 15A continuous and 30A peak current
- 4 encoders
- 20kHz sampling and update rate of all control loops
- Digital I/O
- 8/8 general purpose inputs / outputs
- 4 Registration Mark inputs, 2/8 PEG outputs (Pulse/States)
- 3 motor brake outputs 24V/1A
- Analog I/O: 8/2
|
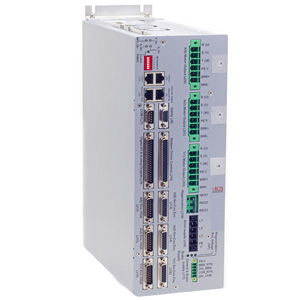 |
The UDMHP/BA is a state of the art series of EtherCAT drive modules with three built-in universal drives. It addresses the needs of modern machinery for both economical and for high performance, scalable and distributed control for motion centric applications.
The UDMHP/BA operates as an EtherCAT node under any SPiiPlus EtherCAT master Controller including the PC based SPiiPlusSC Soft Controller.
The UDMHP/BA addresses high accuracy demanding applications, while the UDMHP/BA econo version addresses more price sensitive applications.
The UDMHP/BA are complemented by the SPiiPlus NT suite of software tools that minimizes network configuration and drive set up efforts and time to market.
The built-in drives are offered with three current levels: 5/10A, 10/20A and 15/30A ((cont./peak).
The modules are powered by a single or three-phase AC from 24 to 265Vac (rectified internally to generate a Vac x 1.4 motor voltage) and by a separate 24Vdc control supply that keeps all low voltage signals alive during emergency conditions. It supports a wide range of position feedback devices: incremental digital, analog SIN-COS, and absolute encoders.
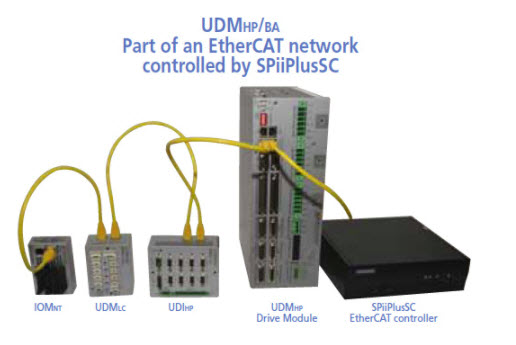
Servo
A standard comprehensive set of powerful algorithms to enhance accuracy, move & settle time, smooth velocity, stability and robustness.
• Advanced PIV cascaded structure
• Loop shaping filters
• Gain Scheduling
• Gantry MIMO control
• Dual feedback / loop control
• Disturbance rejection control
Optional Servoboost® algorithem that provides better, more consistent servo performance, insensitive to noise and large changes in the system.
Drives
Type: digital current control with field oriented control and space vector modulation.
Current ripple frequency: 40 kHz Current loop sampling rate: 20 kHz.
Programmable Current loop bandwidth: up to 4kHz, will vary with tuning & load parameters.
Commutation type: sinusoidal. Initiation with and without hall sensors.
Switching method: advanced unipolar PWM.
Protection: Over voltage, Phase-to-phase short circuit, Short to ground, Over current, Over temperature, motor over temperature.
Current sensing: CMba: 12b ADC, CMhp: 16b ADC.
Power Supplies
The module is fed by three power sources. A motor AC supply, a 24Vdc control supply and 24Vdc motor brake supply.
During emergency conditions there is no need to remove the 24Vdc control supply.
Motor Supply Control supply Motor Brake supply
Range: 85 to 265Vac 24Vdc ± 10% , 4A 24Vdc ± 20% , 3A
Optional Low Voltage operation
(17-85 Vac or 24-120Vdc)
Motor Type
Two- and three-phase permanent magnet synchronous (DC brushless/AC servo), DC brush, Voice coil, Two- and three-phase stepper (micro-stepping open or closed loop) AC induction*.
(* Consult ACS)
Feedback
Incremental Digital Encoder: Four, A&B,I; Clk/Dir,I RS-422. Max. rate: 50 million encoder counts/sec., Protection:Encoder error, not connected
Sin-Cos Analog Encoder (optional): Three.1Vptp, differential.
Multiplication factor: From x4, to-BA: x4,096 HP-x65,536
Maximum frequency: 250kHz
Automatic compensation of Offset, Phase and Amplitude
ADC used: UDMba: 12b, UDMhp: 16b low S/N
Maximum acceleration: 108 million sine periods/sec2.
Protection: Encoder error, not connected.
Hall inputs: Three sets of three per axis. Single-ended, 5V, source, opto-isolated.
Input current: <7mA.
Absolute encoders (optional): Three, EnDat 2.1/2.2, Smart-ABS, Panasonic, Biss-C
5V feedback supply: Total current available for feedback devices: 1A.
Digital I/O
Safety Inputs: Left + right limit per axis, E-stop, General Purpose Inputs: 8 Single-ended,
5Vdc (±10%) or 24Vdc (±20%),opto-isolated, sink/source, Input current: 4-14mA.
Registration Mark inputs: Four. RS422.
Motor Brake Outputs: Three. 24V, 1A ,opto-isolated. Powered by the 24V Brake Supply.
General Purpose Outputs: Eight. Single-ended, 5Vdc (±10%) or 24Vdc (±20%), opto-isolated, sink/source, 100mA
Position Event Generator outputs (PEG): Two PEG_Pulse and eight PEG_State, RS422.
Can be used as general purpose outputs.
HSSI channels: Two. RS422.
Analog I/O
Inputs: Six ±10V, differential, 20kHz sampling rate. The inputs can be used as feedback to the servo loops. Resolution: CMba - 12b, CMhp - 16b. Joystick inputs: two single-end, ±10V, 12b resolution Outputs: Two, Single-end, ±10 V ±5%, 10 bit resolution
Communication
EtherCAT: Two, In & Out, 100 Mbit/sec, RJ45 connectors
Environment
Operating: 0 to +40°C. Storage : -25 to +60°C.
Humidity: 5% to 90% non-condensing
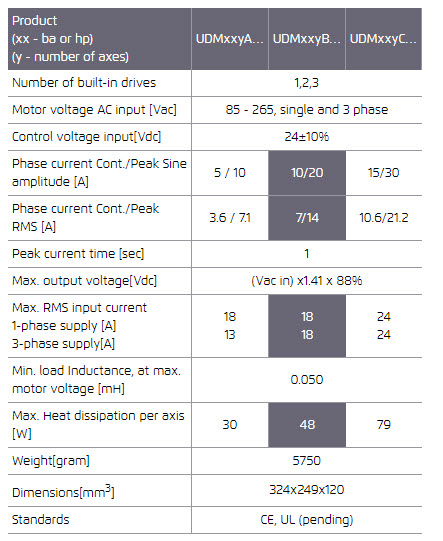
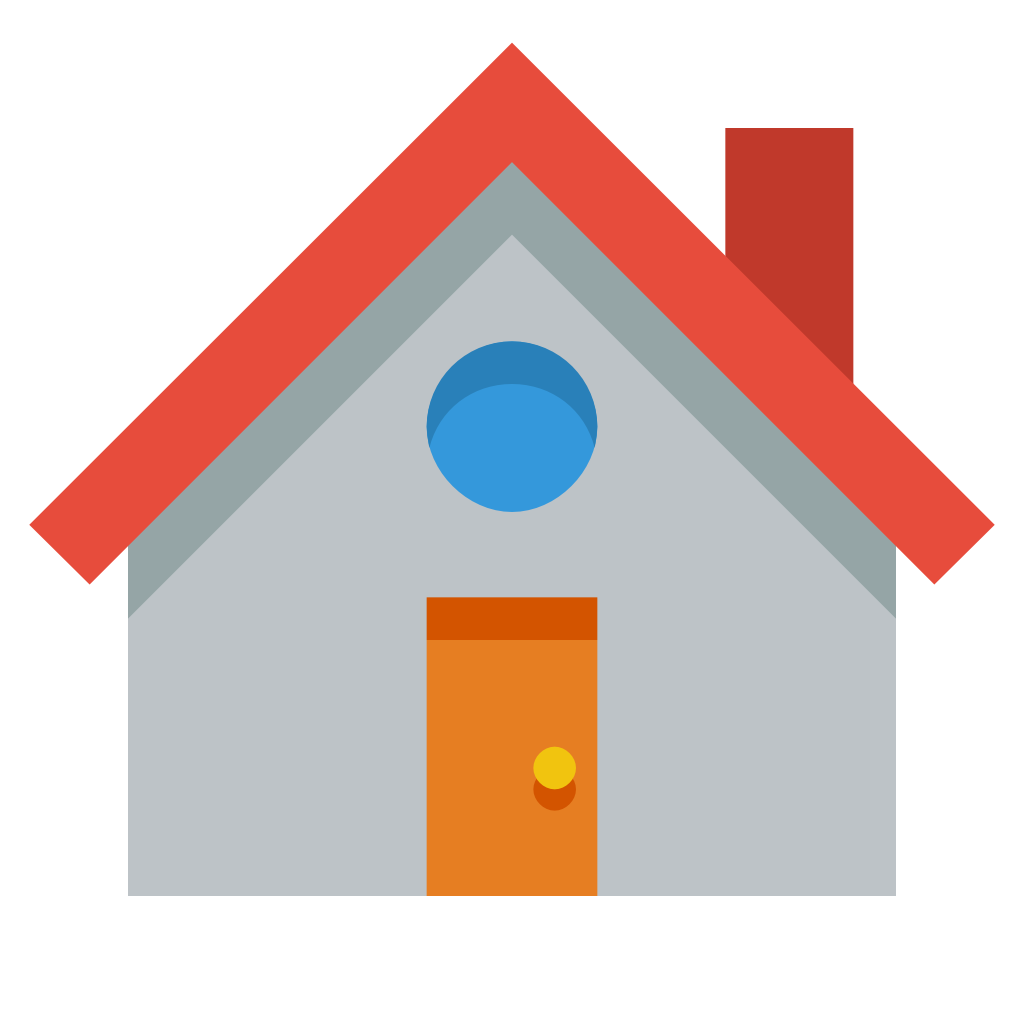 |